How Kraft Heinz is using artificial intelligence to produce a better Claussen pickle
The Claussen pickle brand traces its roots back more than 150 years ago to an Illinois farmer named Claus F. Claussen who had a truckload of cucumbers he couldn’t sell. Instead of tossing them, he turned them into pickles.
Today, making pickles is a big business. Brand owner Kraft Heinz processes approximately 60 million cucumbers annually to make roughly 42 million jars of Claussen, the country’s top-selling refrigerated pickle brand. But making the crunchy spear isn’t always easy.
The cucumbers that turn into Claussen pickles move from vine to brine in 10 days or fewer, giving Kraft Heinz little room for error. It’s paramount that Kraft Heinz knows what the cucumbers coming into the Claussen plant in Illinois look like so it can prepare — varying circumferences, lengths and bends can wreak havoc on planning and require changes to the production line where the spears are processed.
In recent years, Kraft Heinz has incorporated artificial intelligence across many facets of its supply chain to increase efficiencies and wring out costs. Cucumbers and its Claussen pickles brand have been among the biggest beneficiaries of the once-futuristic technology.
Bill Durbin, the head of North America logistics and planning at Kraft Heinz, sat down with Food Dive to discuss the impact of artificial intelligence on the company’s supply chain and Claussen, one of its top-selling consumer brands in its respective category.
This interview has been edited for brevity and clarity.
FOOD DIVE: How did Kraft Heinz get to the point where it could implement AI in its supply chain?
BILL DURBIN: When we talk about the overall company transformation, … the supply chain played a very critical role within that, making sure that we're continuing to evolve to drive efficiencies, to then be able to reinvest back into marketing and into our businesses to be able to continue to grow revenues and improve our performance.
For the supply chain transformation itself, I think as we started, it was really about getting brilliant at the basics and improving our processes and identifying best practices, then rolling that out across our 60 manufacturing facilities, warehouses and distribution centers. And so a very manual effort to get us there, but we saw a lot of benefits by identifying the best way to do something and then standardizing that across and continuing to raise that bar.
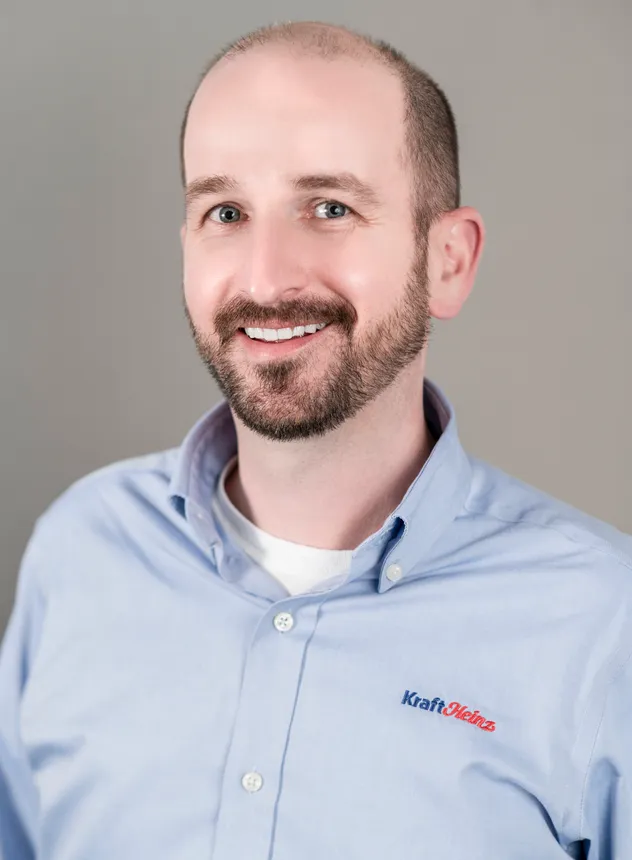
Bill Durbin, head of North America logistics and planning at Kraft Heinz,
Permission granted by Kraft Heinz
But over the last few years, we really kicked off this digital journey where we've been able to accelerate that transformation. By leveraging better tools and improving the visibility of exceptions that happen within the network, and then leveraging things like machine learning, we've been able to get people out of those manual transactions so that they can then help drive further optimization of the supply chain, versus having to be in that day to day transaction.
When did Kraft Heinz first start using AI for cucumbers and how did the idea come about?
DURBIN: We started this about a year ago. Our cucumber supply chain is a very short one. It's 10 days from the field to when it comes into the jar. During certain times of the year, we source cucumbers from fields closer to the manufacturing facility, and during the winter, we source from warmer regions which leads to longer transit time. In a lot of our processes, we can buffer with inventory if the goods are received and they're not exactly the specification.
There are ways to mitigate that, but with such a short supply chain, it's super important that we identify issues as fast as possible and then make sure that we get the sizing correct so we can get the best efficiency as we run those things down the line. This allows us to get the best quality cucumber and the best quality pickles at the end.
With pickles, the circumference matters, the size matters, the length matters, the bend of the cucumber, all of those things, depending on what they are, we will operate differently within the site, as well as quality. If the quality does not meet our specifications, we can't run it.
We started by bringing in batches of cucumbers, taking pictures of those batches and the quality team was getting the feedback on which ones were to specification, like validating, sizing them. We were training the machine to do that same task.
Similar to that prior example, over time, we trained and then saw different types of defects, different types of sizes, what those things meant. And then [AI] learned from that, beginning to identify these variations, and the operator would validate those things. So now it's able to identify those things on its own.
By being able to do that, we can, by having that level of certainty on what that product is, we can address that right away so we know where to send it within the factory, or if it's an issue, we can get that real-time feedback to the suppliers to be able to address.
Today, we're doing this at the factory where the cucumber becomes a pickle in the jar that goes in the case, and we're starting to explore how we introduce this technology earlier in the supply chain so it's where the cucumber goes on the truck. There we get more time or more responsiveness on being able to work with the supplier or to identify the sizes coming in so that we can schedule the factory correctly for those different sizes.
How is this benefitting Kraft Heinz and Claussen?
DURBIN: On pickles, specifically, we've seen, since we put this in place, we've seen a 12% increase in efficiency from that. By being able to make this process and identify these things, we've been able to make sure that the pickles are getting routed to the right place to give us the best efficiency possible, and also to give that feedback to the suppliers.
We are getting better quality from the start. That's allowed us to get more cases out of that factory as we've improved that efficiency, which means better service for our customers.
Are you using a similar process for any of the commodities Kraft Heinz uses?
DURBIN: We're starting to look at those opportunities as well, so we haven't put them in place. For tomatoes, it's the size, it's the color. And so we're looking at tomatoes, potatoes for Ore-Ida French fries on how we can now scale this across those other operations. This was really about building this. There was, to be honest, almost a greater need on the cucumber because of how truly short that shelf life is.
Source link